What is chemical process simulation?
Process simulation includes the illustrative demonstration of structures restricted in range as one PID loop control to those as broad as a complete production capacity. Software-based models permit an extensive range of features to consider. Some considerations are piping capacity and pump speed to chemical reaction rates, and controller responsiveness. Process simulation aims to create a safe, virtual atmosphere. The atmosphere helps test each of those features. They are then advanced across a complete variety of production levels.
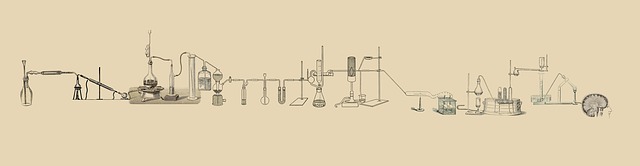
Process simulators help manufacturers to imitate hazardous systems. They are important production atmospheres with changes that look like the real thing. The safe atmosphere provided through simulation is essential while planning a fresh system and new operations staff.
Once a basic manufacture process is recognized, it is rare for engineers to use a process simulator in the analysis of ‘what if’s.’ Those and limitless other ‘what if’s’ can be discovered quickly with the use of a simulator, rapid the period from an idea and example to production and advantage.
Process simulations help practitioners change the sense of awareness for their production processes. As I have noted before, the simulation works like the real McCoy. As staff relates with the simulation, they increase a clearer understanding of how it responds to different working levels and even sudden changes. That training method delivers the best foundation for regular and irregular plant processes.
Security is highly prioritized in most line lines of operation. Given the difficulty and dangerous environment of manufacturing, process simulation is progressively crucial to safety and achievement.
Some businesses form successful industries by licensing powerful simulation answers to various universities and industrial giants. The control station suggests a collection of simulation gears that can help process manufacturers make complete informed choices for improving their production processes’ performance. This is where the control station gets its start.